
Enstone, comté d’Oxford. Sur les routes étroites qui nous emmènent à travers champs, rien ne laisse entrevoir que l’un des monstres sacrés du sport automobile y terre ses installations les plus secrètes et les plus coûteuses. Bienvenue dans la vallée de la formule 1!Etabli en 1992 par Benetton après avoir repris l’écurie Toleman, le centre d’Enstone a été exploité par Renault depuis 2000. Onze ans plus tard, la marque au losange quittait les lieux au profit de Lotus F1 Team, préférant se cantonner au rôle de motoriste. Concentrées sur le site parisien de Viry-Châtillon, les activités sportives de la marque n’allaient pas rester longtemps privées d’Enstone, puisqu’à la fin 2015, Carlos Ghosn a voulu redonner les moyens au losange de se battre au plus haut niveau.
D’un à deux cycles
Depuis le rachat de Lotus et le retour à Enstone au début 2016, trois années se sont écoulées. Conscients de l’immense challenge qui s’annonçait à eux, les dirigeants de l’écurie s’étaient fixés trois ans pour gagner, avec une saison 2016 destinée à rebâtir leur force de frappe avant d’espérer remporter plusieurs podiums en 2017.Dans les faits, bien que les progrès de l’écurie française se soient avérés évidents, ils sont restés en-deçà des projections. 9e du championnat en 2016 avec 8 points – la faute à une monoplace héritée de Lotus, initialement conçue pour le moteur Mercedes –, Renault a commencé à redresser la barre en 2017 (6e avec 57 points), mais sans podium. Au moment de clôturer la saison 2018, le losange pointe à la 4e place (114 points) avant le Grand Prix d’Abou Dhabi, Carlos Sainz et Nico Hülkenberg s’étant chacun distingués par une 5e place comme meilleur résultat, le premier en Azerbaïdjan, le second en Allemagne. Un gouffre sépare donc toujours l’équipe d’Enstone et Viry-Châtillon face aux trois mastodontes que sont Mercedes, Ferrari et Red Bull. D’où l’observation d’un discours modifié, et plus modeste, de la part des patrons de l’écurie en cette fin d’année: au lieu de servir à gagner, les trois premières saisons auront en réalité mis en lumière l’ampleur des efforts à consentir avant une seconde série de trois ans, de 2019 à 2021, pour lancer une véritable offensive.
Renault montre patte blanche
Mauvaise foi, ou sincère prise de conscience que la tâche était nettement plus ardue que prévu? Pour Rob White, directeur des opérations à Enstone depuis 2017 après avoir travaillé à Viry-Châtillon dès 2004, il s’agit d’une preuve supplémentaire que la marque n’a en rien renoncé à son ambition. «Lorsque nous sommes revenus à Enstone, l’équipe était sur les genoux. D’un team aux abois, il a fallu trois ans pour en faire une équipe efficace. Nous sommes à la fin de cette première phase d’amélioration, nos outils sont prêts. Il faut maintenant les mettre à profit», explique-t-il. De quelque 300 collaborateurs à la fin 2015, le nombre d’employés a ainsi doublé, passant à 680. Composé de 22 nationalités, le personnel profite d’une usine rénovée à hauteur de 50 millions d’euros, avec un gain de superficie d’environ 2000 m2. Conçu pour construire une monoplace depuis zéro sous la direction exécutive de Marcin Budkowski, le centre d’Enstone a été passé au crible pour devenir compétitif. «Il nous faut mettre à profit toute cette puissance de feu en matière de personnel, de puissance de calcul et de création», poursuit Rob White. Avant d’admettre: «Nous ne sommes pas satisfaits des performances de nos voitures à l’heure actuelle. A l’interne, nous n’avons jamais été aussi effi caces, mais les points se gagnent sur la piste.»
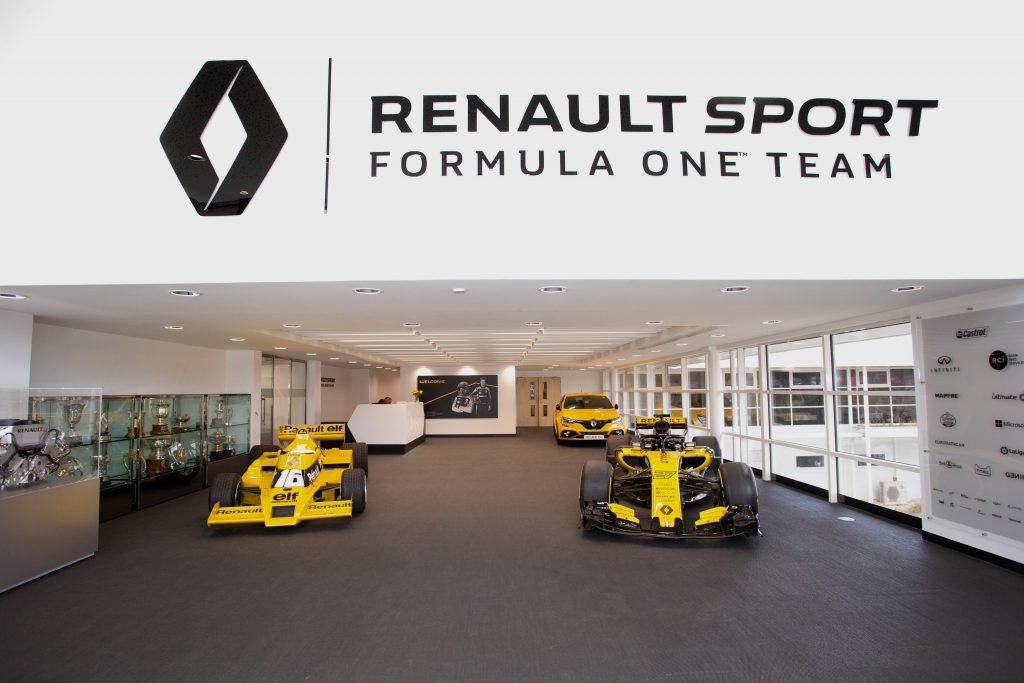
Les bonnes cartes
A raison d’un budget de 300 millions d’euros par an, l’équipe Renault arrivera-t-elle au sommet de la hiérarchie avant les changements de règlements attendus en 2021? Rob White veut y croire. «C’est un challenge énorme. Mais le jeu est le même pour tout le monde. Rien n’interdit de rejoindre Mercedes au meilleur niveau. Ferrari l’a quasiment fait. Je pense cependant que nous avons fait de bons progrès, mais pas assez.»Le Britannique termine en évoquant le dernier atout en date dans la manche de l’équipe, incarné par Daniel Ricciardo. «C’est l’un des meilleurs pilotes du plateau, en plus d’être un attaquant exceptionnel. Le fait qu’il nous rejoigne est un immense vote de confiance.»
BUREAUX D’ÉTUDE
Les bureaux en open space du site d’Enstone accueillent près de 70 ingénieurs chargés de concevoir tous les composants de la voiture. Partagés entre l’amélioration de la monoplace en cours et la création du modèle 2019, ces spécialistes de la conception assistée par ordinateur (CAO) travaillent sans relâche pendant 18 mois afin de mettre au point les quelque 19 000 modèles de pièces requis pour définir les 14 500 composants d’une formule 1. Le nombre total d’heures de travail est estimé à plus de 150 000.
CNC MACHINING
Pour produire plus rapidement les pièces les plus volumineuses de la voiture, Enstone a fait l’acquisition de deux machines-outils à commande numérique (CNC) en provenance du spécialiste italien Breton, chacune valant 1,5 million d’euros. Ces deux centres d’usinage à cinq axes sont à même de fabriquer les composants en carbone, notamment les pièces maîtresses du châssis 2019, lesquelles ont requis 5 mois de travail. Pour garantir la stabilité de la fibre de carbone, la température est maintenue à 20 °C dans les locaux pendant toute l’année.
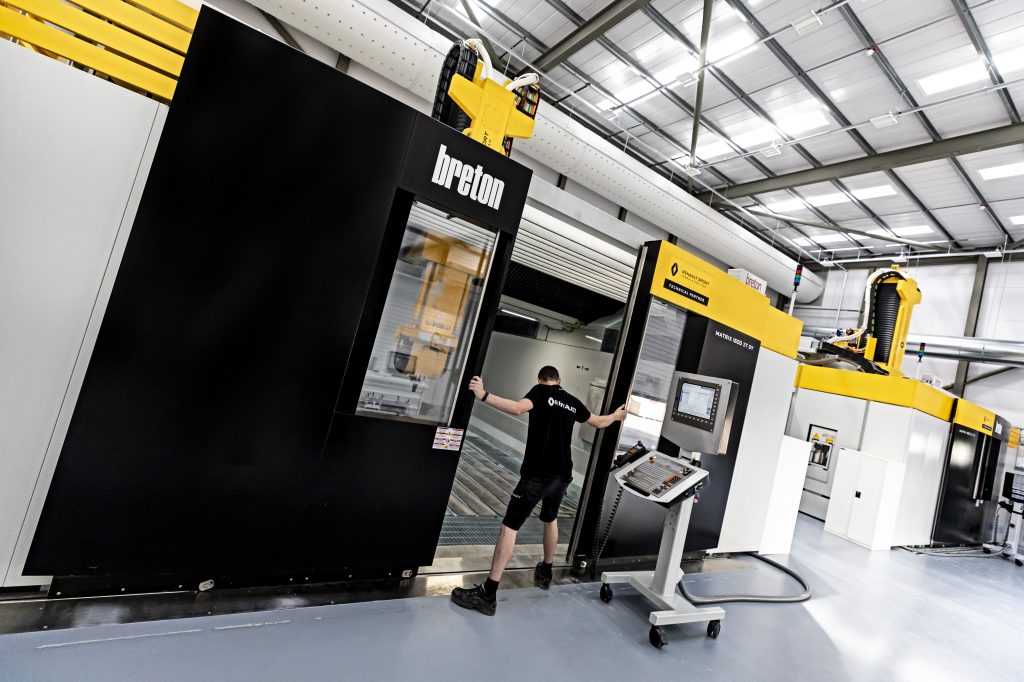
BANCS D’ESSAI ET SIMULATEUR
Pour compléter les vraies séances d’essais lors des Grand Prix, Renault utilise un banc d’essai à vérins dotés de 7 actuateurs hydrauliques destiné à reproduire le travail des suspensions. En parallèle, mis en service en 2011, le simulateur de Renault F1 tourne sur le logiciel rFactor Pro via une modélisation de la voiture faite maison. A l’heure actuelle, l’infrastructure est par exemple mise à profit pour tester la meilleure valeur d’empattement pour la voiture de 2019. L’alimentation électrique du système est fournie aux trois quarts par des panneaux solaires, dont la capacité annuelle avoisine les 33 000 kWh.
ADVANCED DIGITAL MANUFACTURING
Utilisée dès 1998 à Enstone, la fabrication de pièces couche par couche s’est nettement intensifiée au sein des écuries de F1. Au moment de notre visite, pas moins de 6 imprimantes 3D tournaient à plein régime pour produire environ 600 pièces par semaine, certaines étant utilisées directement sur les monoplaces, d’autres servant aux modèles réduits testés en soufflerie. Très utile pour produire des formes rondes complexes, l’impression 3D de Renault utilise un alliage à forte teneur en nickel et en carbone, baptisé Iconel et emprunté à l’aviation. Auparavant, les plastiques utilisés étaient trop sensibles à l’humidité.
ATELIERS
Outre les monoplaces de la saison en cours, les voitures utilisées en 2016 et 2017 sont maintenues en parfait état de marche, notamment dans le cadre des tests pour jeunes pilotes. Avant le stockage des pièces, une nouvelle «clean room» permet également de vérifier la pureté de chaque composant grâce à une machine à rayons X.
AÉRODYNAMIQUE
Mise en service en 1998 et modernisée en 2017, la soufflerie de 2674 m2 ne peut être utilisée qu’à raison de 65 cycles par semaine, avec un flux d’air restreint à 50 mètres par seconde, selon le règlement de la FIA. La taille du modèle de la voiture ne doit pas dépasser 60%, mais celui-ci dispose de «vrais» pneus Pirelli à échelle réduite. Bardée de capteurs et suspendue en l’air via une tige métallique, la réplique de monoplace pivote sur les axes de roulis, tangage et lacet pour simuler le comportement en virage. En parallèle, un superordinateur composé de 3000 processeurs, installé sous terre depuis 2008, produit plus de 60 teraoctets de données chaque semaine pour simuler le comportement des nouvelles pièces par CFD (mécanique des fluides numérique).
SALLE DES OPÉRATIONS
Coeur stratégique d’Enstone depuis sa création en mai 2017, la pièce baptisée «Ops room» est réservée à 24 ingénieurs triés sur le volet. En même temps qu’une seconde salle du même type à Viry-Châtillon, Enstone assiste les ingénieurs du circuit dans leurs prises de décision en analysant la course sur six écrans de 75 pouces, sans compter les 24 ordinateurs bi-écrans. Chaque seconde, les quelque 200 capteurs installés sur les deux monoplaces fournissent 150 000 mesures quasiment en temps réel, quel que soit l’endroit du globe (moins de 0,05 seconde).