Lorsque, à Sant’Agata Bolognese, près de Modène, on se met à produire des masques de protection en lieu et place de Huracan, Aventador et Urus, il y a de quoi se poser des questions. Volkswagen, la maison-mère, diversifie aussi ses activités en produisant des masques, de même que la filiale espagnole Seat, qui s’est lancée en plus dans la fabrication de respirateurs. Le nouveau coronavirus, qui est parti de Chine et paralyse désormais le monde entier, est en train de chambouler une industrie automobile d’ordinaire plutôt circonspecte.
En quelques semaines, de nombreux constructeurs automobiles se sont convertis à la production d’équipements médicaux pour répondre à la croissance soudaine de la demande.
Conversion des lignes de production
Le groupe VW s’est lancé dans la fabrication de produits médicaux sur différents sites en Europe. Ce faisant, il exploite en partie des capacités qui ne peuvent plus être utilisées pour l’assemblage d’automobiles en raison de l’arrêt général de la production. Les imprimantes 3D, qui permettent de produire rapidement et à moindre coût de nouveaux composants pour les appareils médicaux, jouent également un rôle important.
La filiale espagnole, Seat, est celle qui va le plus loin en matière de production d’équipements. Des appareils respiratoires sont assemblés à l’usine de Martorell, près de Barcelone. Sergio Arreciado, du département technique des procédés, donne quelques précisions: «La conversion d’une chaîne de montage automobile à la production de ventilateurs de réanimation a été difficile, mais nous l’avons fait en un temps record.»
Le nouveau ventilateur de Seat est constitué de plus de 80 composants électroniques et mécaniques. A la base, il s’agit du modèle Oxygen de Protofy (lire l’interview). Il est animé par un moteur d’essuie-glace modifié. Le système d’entraînement comprend également des pignons que Seat produit au moyen d’imprimantes 3D, ainsi que des arbres de transmission. Le contrôle de la qualité, en fin de chaîne, comprend un poste de stérilisation par rayonnement UV.
Collaborateurs flexibles
«A chacun son métier», dit l’adage. Mais d’où est donc venue cette nouvelle compétence? Chez Seat, plus de 150 employés de différents services ont été impliqués dans le développement des ventilateurs: «De l’ingénieur au directeur de la production, en passant par l’équipe de sécurité et de santé, souligne Christian Vollmer, vice-président en charge de la production et de la logistique. Le projet a été rendu possible grâce à une équipe d’ingénieurs exceptionnels, ajoute-t-il. La compétence et la créativité ont finalement conduit à l’utilisation de notre moteur d’essuie-glace et de nouvelles pièces produites par imprimantes 3D.»
A Martorell, on est fier de ce nouveau produit: «Seat est le premier constructeur automobile à codévelopper des respirateurs et à les produire dans ses usines. Mais il est également crucial que ce savoir-faire soit partagé. L’information est librement accessible, de sorte que d’autres industriels de divers pays peuvent convertir, eux aussi, leur production.»
Masques de protection improvisés
Le matériel médical fabriqué par Lamborghini, une autre filiale du groupe VW, est techniquement moins complexe. La manufacture de voitures de sport produit 1000 masques de protection par jour. C’est le secteur de la sellerie, normalement en charge de l’aménagement intérieur des coûteuses voitures de sport, qui est chargé de cette nouvelle tâche. En France, plusieurs entreprises industrielles ont constitué une alliance à la demande du gouvernement. Celle-ci réunit notamment le groupe automobile PSA, l’équipementier Valeo et Air Liquide, un important producteur de gaz techniques. Divers produits médicaux sont fabriqués dans plusieurs usines.
Les Britanniques ont également recours à des méthodes inédites pour assurer un approvisionnement suffisant de leurs hôpitaux. Le fabricant d’aspirateurs Dyson, par exemple, produit désormais des respirateurs. L’appareil, qui s’appelle Covent, a été développé en seulement dix jours, car Dyson a pu s’appuyer sur des technologies déjà disponibles.
The american way
L’usine General Motors de Kokomo, au nord d’Indianapolis, s’est également lancée dans la production de masques de protection et de respirateurs. Bien que le géant automobile américain considère la fabrication de ventilateurs comme «très complexe pour des entreprises extérieures à ce secteur», il en produira jusqu’à 10 000 unités par mois pour Ventec Life Systems, dès mi-avril. GM forme actuellement plus de 1000 de ses salariés et du personnel local spécialement recruté à cette fin. «Chaque appareil nous aide à sauver des vies. GM, le syndicat automobile UAW et la ville de Kokomo collaborent à ce projet», explique Gerald Johnson, vice-président exécutif de GM Global Manufacturing. Et Mary Barra, PDG du groupe, enfonce le clou: «Les équipes travaillent avec une passion et un engagement incroyables.»
Les règles en vigueur sont strictes. Avant de se mettre au travail, les employés sont tenus de se laver les mains; ils doivent, en outre, se faire relever la température et porter obligatoirement le masque. Et, au moment des changements d’équipe, des intervalles de 30 minutes sont prévus pour nettoyer les postes de travail. Il va de soi que la distance sociale s’applique partout, elle est d’environ 1,8 mètre aux Etats-Unis. Les boutons de portes et autres «pièges à virus» du même genre sont nettoyés trois fois par équipe, chacune disposant en outre de ses propres entrées et sorties.
En plus de l’appareil multifonctions VOCSN développé par Ventec Life Systems, l’usine de Warren (Michigan) fabrique des masques chirurgicaux. La production doit être portée à 50 000 unités quotidiennes, mais il est possible d’aller jusqu’à 100 000. Il n’est pas surprenant qu’Elon Musk, le patron de Tesla, se soit aussi mis sur les rangs pour apporter son aide. Mais, contrairement à la plupart des autres intervenants, le fabricant de voitures électriques veut produire des ventilateurs en ayant recours, pour l’essentiel, à des composants d’automobiles. L’écran du système d’infodivertissement, par exemple, devient un élément d’affichage et de contrôle, tandis que le boîtier électronique du véhicule contrôle les valves pneumatiques.
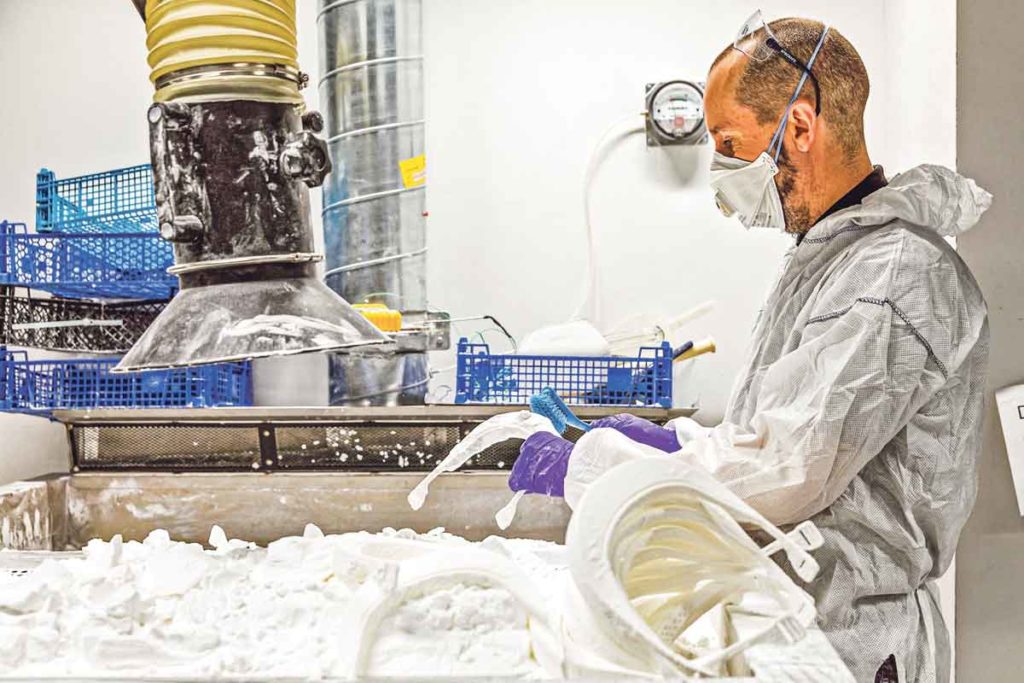
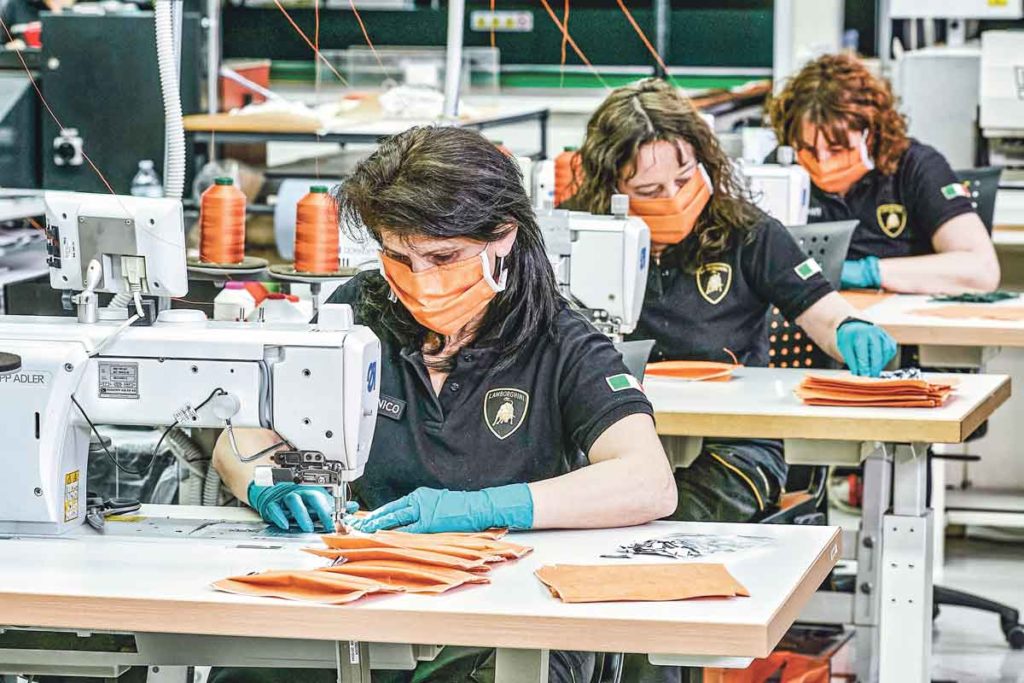
«Jusqu’à 300 appareils par jour à l’usine de Martorell»
Le respirateur Oxygen, développé sous la direction de la start-up Protofy, se distingue par sa conception simple et son faible prix. De ce fait, il peut être mis rapidement en fabrication, même par des entreprises de mécanique étrangères au monde médical. Outre Seat, les partenaires de Protofy comprennent notamment l’usine Renault de Bursa, en Turquie. Le cofondateur de Protofy, Ignasi Plaza, a répondu à quelques questions de la Revue Automobile.
Revue Automobile: Le respirateur Oxygen a-t-il intégralement été développé par Protofy, ou Seat a-t-il joué un rôle majeur dans son développement?
Ignasi Plaza: Oxygen a été conçu, développé et homologué par Protofy. Mais Seat a procédé aux adaptations nécessaires pour que l’appareil puisse être assemblé sur les lignes de production existantes. Des processus similaires ont été menés dans d’autres pays, en collaboration avec des partenaires industriels.
Comment les employés de Seat travaillant à l’usine de Martorell, habitué à de toutes autres tâches en temps normal, ont-ils été formés à leur nouvelle mission?
Le personnel du siège a étudié la documentation fournie par Protofy. Les employés ont ensuite formé leurs propres équipes pour industrialiser le processus. Chaque équipe est responsable d’un domaine spécifique.
Combien d’unités doivent être produites chez Seat?
À Martorell, la production a été portée à 300 unités par jour. Si la qualité des appareils donne pleinement satisfaction, d’autres usines pourront s’y mettre à leur tour.
Quel est le prix d’un respirateur de ce type?
Environ 450 euros, si nous parvenons à la produire en grande série.
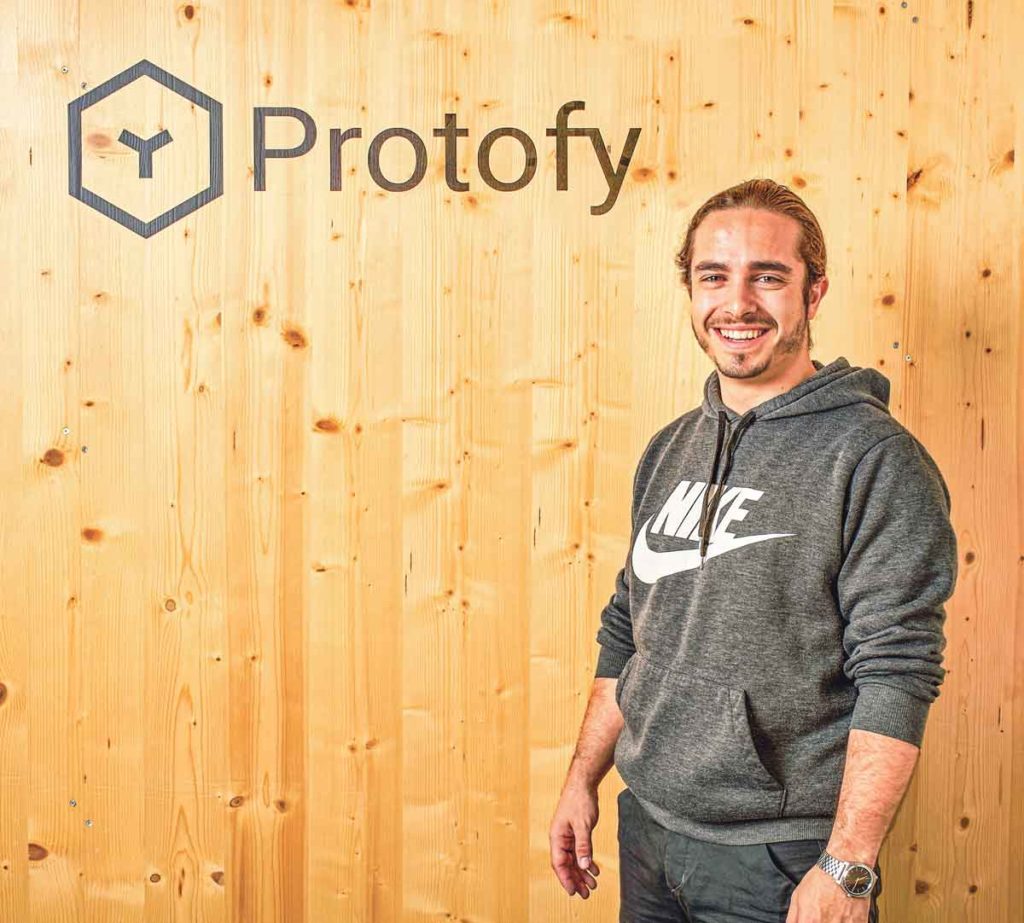