L’avènement de la voiture électrique semble aujourd’hui inéluctable. Considérés par d’aucuns comme la pierre angulaire dans la lutte contre le réchauffement climatique, les véhicules électriques devraient, quoiqu’il en soit, jouir d’un développement à grande échelle dans les années qui viennent. Il est vrai que quiconque se base exclusivement sur la catégorie énergétique des véhicules électriques considérera cette dernière comme le véritable messie de l’écologie.
Mais la voiture électrique est-elle réellement si écologique? Bien sûr, le problème réside dans l’évaluation inique de l’efficience énergétique des véhicules électriques. Effectivement, les autorités ne prennent en compte que les «tailpipe emissions», soit les émissions de polluants à la sortie du pot d’échappement, à l’heure d’établir leur classement énergétique. Evidemment, à ce jeu-là, les véhicules thermiques ne peuvent espérer rivaliser avec les voitures électriques.
Mais, qu’en est-il lorsque l’on prend également en compte la production de matières premières ainsi que la fabrication et le transport des véhicules et des différents composants (ce que l’on appelle le «cradle to gate»)? Eh bien, on se rend bien vite compte que les véhicules à batterie jouissent d’une évaluation préférentielle, et ce sur deux points. Tout d’abord, de par la conception de leurs batteries, ils entraînent irrémédiablement une pollution de l’environnement bien avant leur «naissance». Ensuite, la fabrication des véhicules électriques est, pour l’instant encore, nettement plus polluante pour l’environnement que celle d’un véhicule thermique. A l’avenir, pour pallier ce déséquilibre et ainsi remettre les choses en parité, il faudra nécessairement tenir compte du cycle de vie complet des véhicules (autrement dit le «cradle to grave») et plus seulement les quantités de CO2 émises en sortie de pot d’échappement.
Une évaluation difficile
Reste qu’une détermination fiable des particules et autres gaz émis par les pots d’échappement est des plus complexes à établir, comme le prouvent les discussions au sujet du Dieselgate et l’introduction de la RDE (Real Driving Emissions). Et si l’on tient compte de l’incidence que la production des batteries a sur l’environnement, les procédures d’homologuation vont devenir un véritable casse-tête. Et ce pour la simple et bonne raison qu’il existe un nombre incalculable de paramètres influençant la production, comme le taux d’exploitation d’une usine ou l’endroit où elle se situe (indicateur de la provenance de l’énergie). Etant donné que la production de batteries est une industrie mondiale avec des mines et des sites de production répartis tout autour du globe, chaque fabricant a ses méthodes de production bien à lui. Et, s’il est possible de déterminer avec une fiabilité toute relative les besoins énergétiques d’une usine de batteries, les émissions de CO2 sont, quant à elles, bien plus difficiles à définir. Il y a une énorme différence entre une usine de batteries qui se procure son énergie auprès d’une centrale hydraulique propre et une autre qui se fournit auprès d’une centrale à charbon.
Ironie du sort, le sud de la Chine, où se trouve aujourd’hui une grande partie des sites de production de batteries, peut se prévaloir d’une proportion gigantesque d’énergie hydraulique et, donc, d’une énergie plus propre que dans de grandes parties de l’Europe. Ainsi, les plans d’une alliance européenne pour les batteries visant à rapatrier en Europe la production de batteries dans le cadre du «Green New Deal» aurait, certes, un sens du point de vue économique, mais pourrait même, dans le pire des cas, se révéler préjudiciable pour le climat. En effet, l’Allemagne, la Tchéquie, la Pologne et d’autres pays d’Europe de l’Est restent, encore aujourd’hui, fortement tributaires des centrales fonctionnant au charbon ou au gaz naturel.
Plus d’autonomie, plus de pollution
Jusqu’à quel point une voiture électrique est-elle nocive pour le climat? A l’heure du bilan, il faudra nécessairement prendre en compte le nombre d’accus embarqués; effectivement, chacune des cellules de la batterie engendre son lot d’émissions de CO2. Cela signifie donc que la pollution de l’environnement est directement liée à la capacité de la batterie. En d’autres termes, plus grande est l’autonomie, plus importante est la pollution de l’environnement. A l’échelle mondiale, il n’y a que très peu d’études fiables quant aux besoins énergétiques et aux émissions de CO2 rejetées lors de la production de batteries. C’est que le calcul des chiffres n’est vraiment pas simple.
Une analyse faite par l’organisme londonien «Circular Energy Storage» a calculé que 39 et 200 kilos de CO2 étaient nécéssaires pour produire un seul kWh. Pour une voiture de classe moyenne, par exemple, dotée d’une batterie de 39 kWh, cela se traduit par des émissions de CO2 allant de 1,5 à 7,8 tonnes de CO2 générées lors de la fabrication. Un handicap qui représente une distance allant de 13 000 à 68 000 km pour un véhicule thermique. Bien entendu, plus la batterie est grosse, plus ce handicap est grand. Dans le cas d’une voiture du segment supérieur avec une batterie de 95 kWh, l’empreinte écologique est encore plus lourde, puisqu’avec des valeurs comprises entre 3,7 à 19 t de CO2, une voiture électrique doit couvrir une distance comprise entre 18 000 et 95 000 km avant de devenir un avantage du point de vue écologique.
Nouvelle méthode d’évaluation
Une nouvelle méthode d’évaluation des émissions de CO2 permettrait de pallier cette inégalité de traitement entre les voitures électriques et thermiques. Si, à l’avenir, l’évaluation ne tient pas uniquement compte des émissions de polluants en cours de fonctionnement, mais sur l’intégralité du cycle de vie d’un véhicule, le «greenwashing» écologique entourant les véhicules électriques deviendra immédiatement caduc.
Cela dit, si elles sont fabriquées correctement, c’est-à-dire en utilisant des sources d’énergie renouvelable, les voitures électriques seraient tout à fait en mesure d’être plus propres que les voitures thermiques d’aujourd’hui, et ce sur la totalité de leur cycle de vie.
En conclusion, il est de première importance de ne pas négliger les émissions engendrées lors de la fabrication des véhicules. A l’avenir, si un véhicule est évalué sur l’intégralité de son cycle de vie, cela aura pour effet de loger toutes les propulsions à la même enseigne. C’est là le seul moyen de prendre en considération les avantages et les inconvénients écologiques de tous les «carburants», y compris les carburants synthétiques. Si ceux-ci sont certes énergivores lors de leur fabrication, ils sont également neutres en matière de CO2 étant donné qu’ils captent du CO2 lors de leur production. Aujourd’hui, les carburants diesel comportent une part importante d’hydrocarbures biologiques. Et pourtant, cet avantage n’est pas pris en considération dans le bilan actuel des moteurs à combustion.
La batterie, le nouveau pétrole
GÉOPOLITIQUE Le boom de la voiture électrique a fait des batteries le nouvel «or noir», attirant les convoitises autour des matières premières. La Chine domine la chaîne d’approvisionnement, mais l’UE a décidé de réagir.
Avec la transition vers l’électrification, les batteries des véhicules électriques deviennent un enjeu capital. Malgré une baisse drastique du kilowatt-heure – il est aujourd’hui d’environ 156 dollars, contre 1000 dollars en 2010 –, les accumulateurs sont toujours l’élément le plus cher d’une voiture électrique. Ils représenteraient entre 35 et 40% des coûts de production d’un véhicule électrique (VE). Un rapport de la Commission européenne estime qu’il y aura entre 50 et 200 millions de VE en circulation d’ici 2028 (contre 7 aujourd’hui), représentant un chiffre d’affaires potentiel de 250 milliards d’euros rien que dans l’Union Européenne.
Les pays asiatiques ont flairé le coup à jouer: les leaders mondiaux de la batterie – CATL, Panasonic, BYD, LG Chem, Samsung – sont tous situés en Extrême-Orient. La Commission européenne estime que 85% des accumulateurs proviennent d’Asie. Toutefois, c’est bien la Chine qui mène le bal, elle qui a lancé de lourds programmes d’électrification de sa flotte de véhicules, à partir de 2009 déjà. Des subsides à l’achat de «New Energy Vehicles» (NEV) ont été promulgués à partir de cette date, ce qui a favorisé l’émergence de constructeurs automobiles chinois.
«Obligés de passer par la Chine»
Surtout, l’Empire du Milieu a fait main basse sur toutes les matières premières nécessaires à la fabrication des batteries. «Pendant la crise de 2008, les Chinois ont commencé à acheter les matières premières partout dans le monde, explique Laurent Horvath, géo-économiste des énergies et créateur du site 2000watts.org. Aujourd’hui, si vous voulez fabriquer une batterie, vous devez passer par eux.» Il est question du fameux lithium, que l’on trouve en abondance au Chili et en Bolivie, mais surtout du cobalt. Ce métal, utilisé comme stabilisateur de la cathode et prévenant la surchauffe de la batterie, est concentré en République Démocratique du Congo, qui en produit entre 50 et 70% de la quantité mondiale. La Chine contrôle sept des plus grandes mines de cobalt de la RDC. Aujourd’hui, le tarif de la tonne est redescendu à 28 500 dollars, après avoir atteint un pic en 2018, à 95 000 dollars. Les constructeurs de batteries cherchent, en effet, des alternatives à ce matériau, qui la compose à hauteur de 30%, contre 11% pour le lithium. L’instabilité politique de la RDC pousse aussi à voir «ailleurs», les exploitations minières attisant les conflits. «Pour les minéraux rares, les effets sont similaires au pétrole, l’exploitation minière peut augmenter le risque de guerre, surtout si elle est effectuée par des entreprises irresponsables et que le gouvernement du pays est corrompu», explique Dominic Rohner, professeur d’économie politique et institutionnelle à l’Université de Lausanne.
Réaction européenne
Consciente de ces enjeux, l’Union européenne a lancé «l’alliance européenne pour les batteries (AEB)» en octobre 2017. Le but, créer un pôle européen pour la fabrication d’accumulateurs; 20 à 30 usines de fabrication pourraient voir le jour afin de représenter jusqu’à 25% de la production mondiale de batteries en 2028. «Que ce soit d’un point de vue économique ou d’un point de vue géostratégique, l’UE doit veiller à ne pas devenir tributaire des matières premières primaires et des autres matériaux transformés présents tout au long de la chaîne de valeur des batteries et qui sont d’origine étrangère», lit-on dans le rapport de la Commission européenne. Principal pays visé, la Chine, «qui domine la chaîne d’approvisionnement des batteries lithium-ion». Car l’enjeu s’étend au-delà de la fourniture des batteries, elle porte sur toute l’industrie automobile, qui fait sa mue vers le véhicule électrique. «Derrière le contrôle de la chaîne d’approvisionnement des batteries, c’est le contrôle de la fabrication des automobiles au niveau mondial qui est en train de se jouer», avertit Laurent Horvath. «La Chine a effectivement une opportunité, avec son expertise dans les batteries, de se positionner dans le véhicule électrique», confirme Olivier Perroud, responsable de l’unité mobilité des Services industriels de Genève (SIG). L’Empire du Milieu, partie au pas de charge, a déjà accumulé une importante avance. Aux Européens de répondre, dans la même mesure.
Le bout de la route
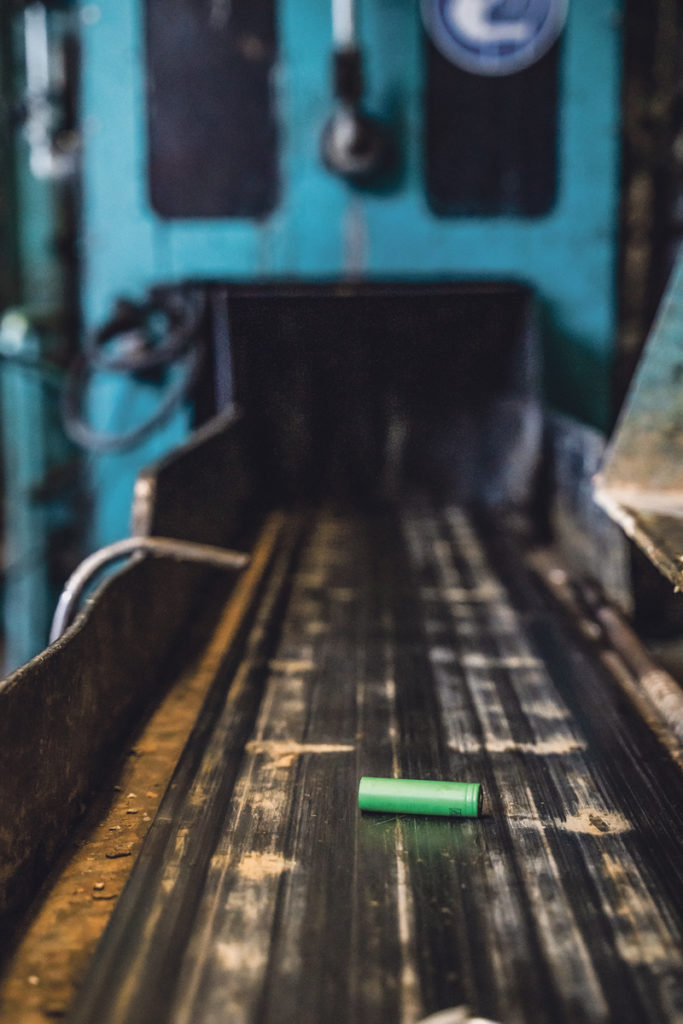
RECYCLAGE En Suisse, le recyclage des batteries est la spécialité de Batrec. Le marché est encore petit, mais ses perspectives de croissance sont gigantesques.
Cela sent l’électrolyte, autrement dit le moisi. L’ambiance y est rude, bruyante, brutale. La chaîne tourne infatigablement à raison de deux ou trois équipes par jour. Où a-t-elle circulé, cette cellule de batterie de Tesla verte, au cours de sa vie? Maintenant, elle n’est plus qu’à quelques mètres du broyeur: Terminus, tout le monde descend, c’est la fin du voyage! Au fur et à mesure que se propagent les voitures électrifiées – en Suisse, avec 21,6% au premier semestre 2020, autant dire que l’on n’en a jamais immatriculé autant –, augmente aussi la nécessité de recycler les batteries haute tension de ces voitures 8 ou 15 ans plus tard.
La société Batrec, à Wimmis, est la seule de notre pays à récupérer les matières premières que contiennent les accus de voitures électriques et hybrides. Pour l’heure, le marché est encore restreint puisque l’usine de l’Oberland bernois ne reçoit chaque mois qu’entre quatre et cinq pack de batteries d’autos électriques ou hybrides. Pour la plupart, elles ne sont pas épuisées, mais elles proviennent de voitures ayant servi à des essais, qui sont impliquées dans des accidents ou qui sont tout simplement défectueuses. «Mais, ces prochaines années, cela va changer du tout au tout», explique le directeur du site, Dieter Offenthaler. La production et, en corollaire, le volume de batteries à recycler vont connaître une croissance exponentielle (cf. graphique). Ce que Batrec recycle d’ores et déjà en quantité relativement importante et régulièrement, ce sont des batteries lithium-ions de vélos à assistance électrique, de smartphones ou tout autre appareil de grande consommation. Logique, le processus de recyclage est commun pour tous ces éléments.
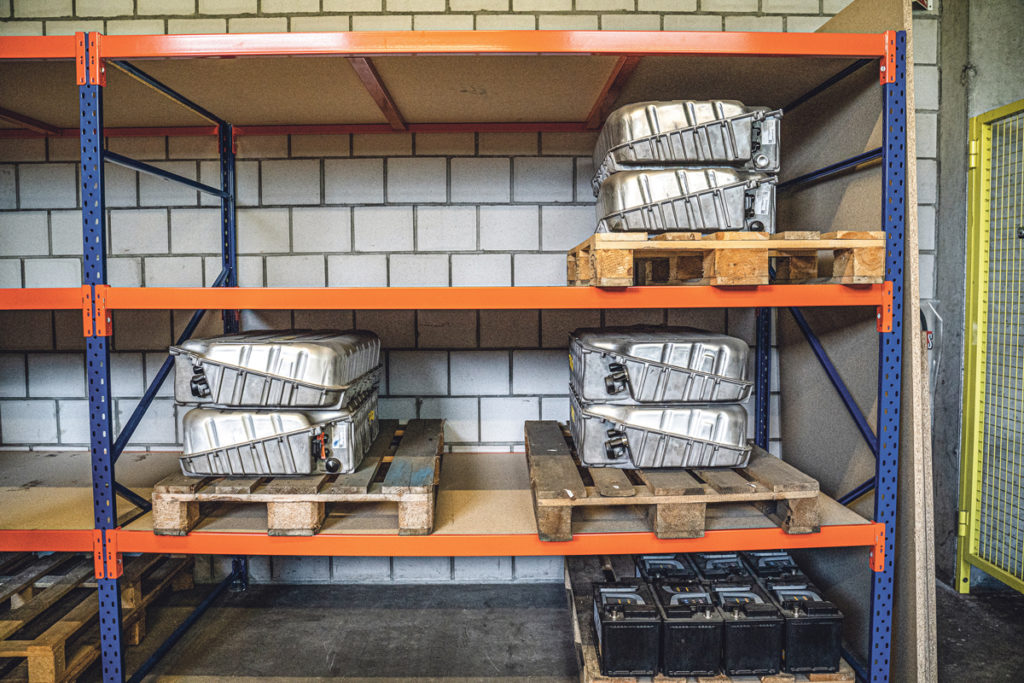
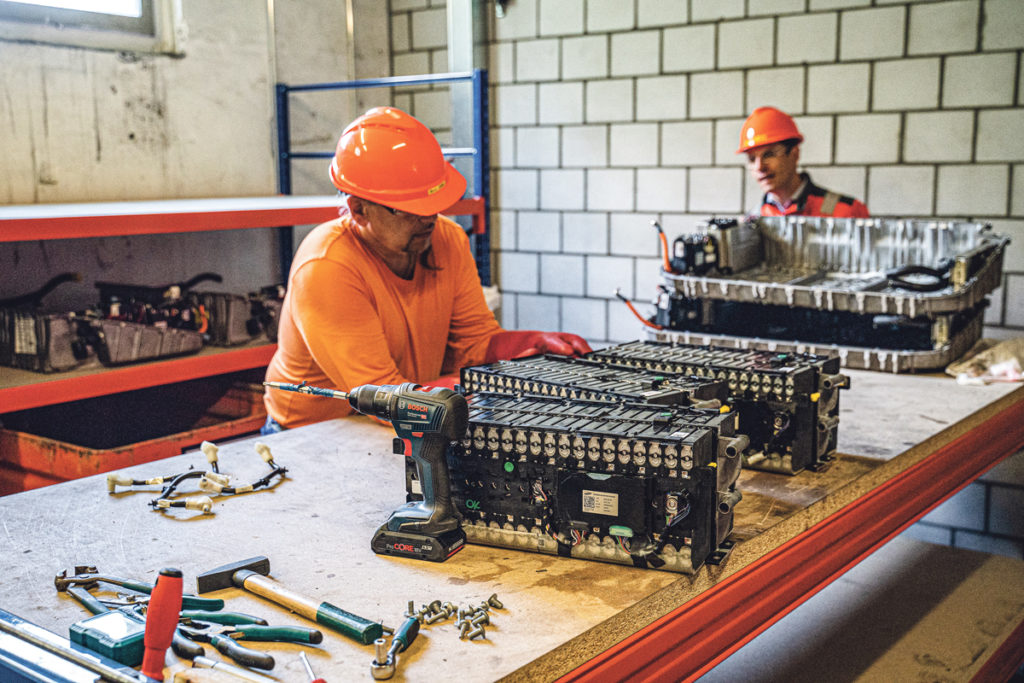
Un site plein de potentiel
Ainsi, dans un futur plus ou moins proche, le site de Wimmis devrait êre agrandi. Et ce afin d’accueillir sur place la totalité des étapes du recyclage. Aujourd’hui, les deux étapes finales se déroulent à l’usine-sœur de Veolia, à Dieuze, à proximité de Metz. «Tout simplement parce que nous n’avons pas encore suffisamment de batteries à traiter pour justifier la mise en œuvre d’un appareillage approprié», précise Dieter Offenthaler. Mais, cela pourrait bien vite changer, Veolia ayant notamment passé un accord avec Renault. Eh oui, toutes les marques doivent savoir où envoyer leurs batteries à l’heure du recyclage.
Parmi les deux étapes que Batrec ne peut accomplir sur place, il y a le tri mécanique des cellules broyées. Ce processus donne naissance à ce que l’on appelle la masse noire qui contient entre autres le cobalt, le nickel ou le manganèse. Ces métaux de transition, ainsi que le graphite dans ce cas-là, sont extraits au cours d’un processus hydrométallurgique, c’est-à-dire en étant trempé dans un bain acide. Une autre méthode de recyclage est celle de la surfusion thermique. Une procédure pyrométallurgique qui permet à Batrec de recycler d’autres batteries comme les accus ménagers par exemple. Contrairement à la batterie ménagère qui est tout d’abord pyrolysée à 700° (ce qui permet à l’eau et au mercure de s’évaporer alors que le papier et le plastique sont carbonisés) et plus tard fondue à 1500°, la batterie de voiture est tout d’abord brûlée et ensuite moulue. Ce processus permet de récupérer le cobalt, le nickel et le cuivre. En revanche, cela ne permet pas de recycler le lithium, le graphite, l’aluminium ou l’électrolyte.

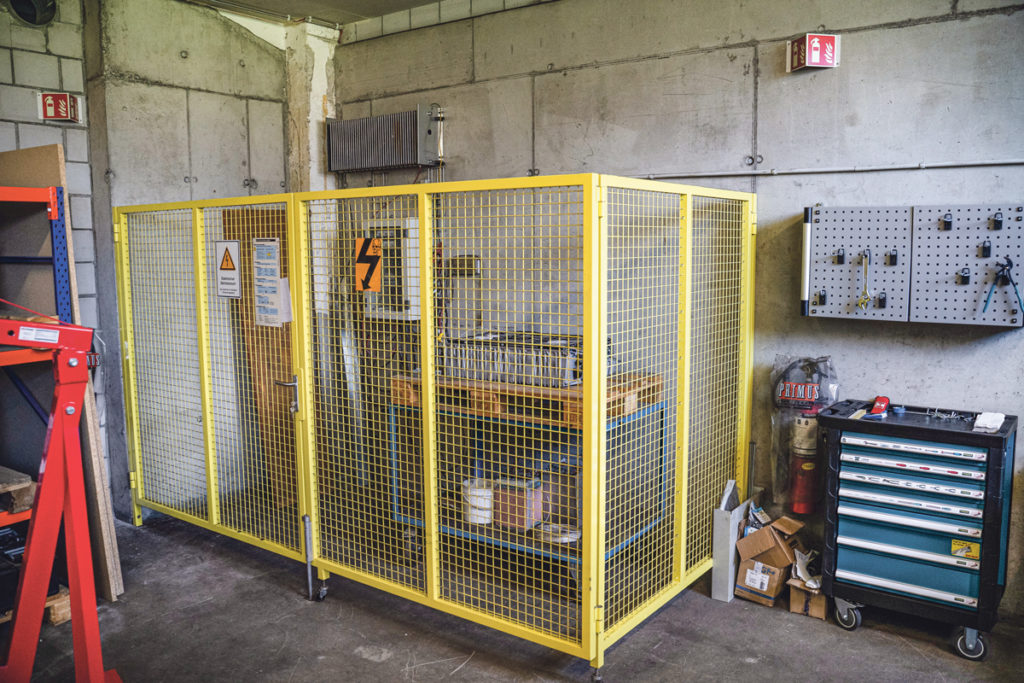
En fin de compte, le processus de recyclage d’une batterie n’est ni plus compliqué ni plus générateur de CO2 que bien d’autres choses. Tous les gaz de fumée et eaux usées inhérents au processus sont épurés selon un procédé sophistiqué. Chez Batrec, tout le courant consommé par le site est originaire d’énergie hydraulique renouvelable.
On ne recycle pas le lithium
Chez Batrec, comme chez beaucoup de ses concurrents, on ne recycle pas le lithium. «Il y en a assez dans le monde et les batteries n’en comportent que très peu. Un accu lithium-ions ne contient qu’entre 1 et 2% de lithium», développe Dieter Offenthaler. De plus, le lithium recyclé doit être extrêmement pur pour pouvoir être utilisé. La société allemande Duesenfeld, située non loin de Braunschweig, a mis au point un procédé permettant de recycler du lithium réutilisable. Bien évidemment, dès que la quantité de batteries à recycler sera de l’ordre de centaines de milliers de tonnes, tous les spécialistes recycleront le lithium. Ne serait-ce que pour des questions d’image.
Avant de partir en France à l’usine-sœur pour leur traitement final, les accus broyés subissent encore une étape à Wimmis: ils sont démantelés. «C’est l’étape la plus compliquée.» Les modules soudés ou vissés sont extraits à la main de leur carter en aluminium. Exactement comme l’on extrait plus tard les cellules hors des modules. Etant donné que les formes, la nature et le traitement des paquets de batteries varient fortement d’un constructeur à l’autre, cela rend impossible tout processus standardisé ou, a fortiori, robotisé. «Dans le cas d’une batterie de Tesla de 100 kWh, cela représente entre quatre et cinq heures de travail manuel», dit Offenthaler.
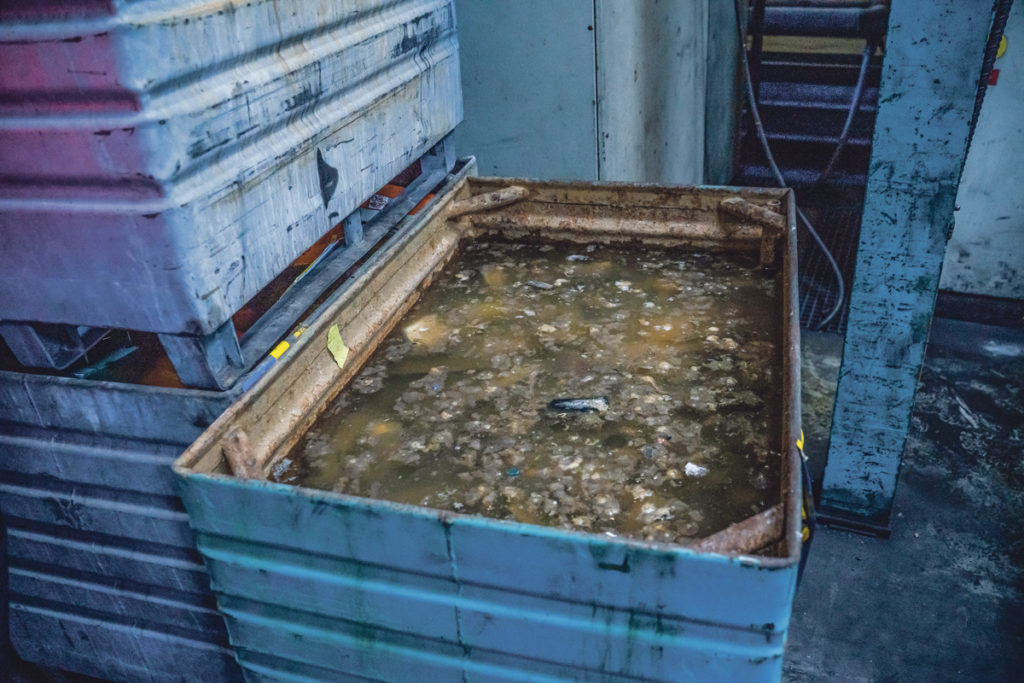
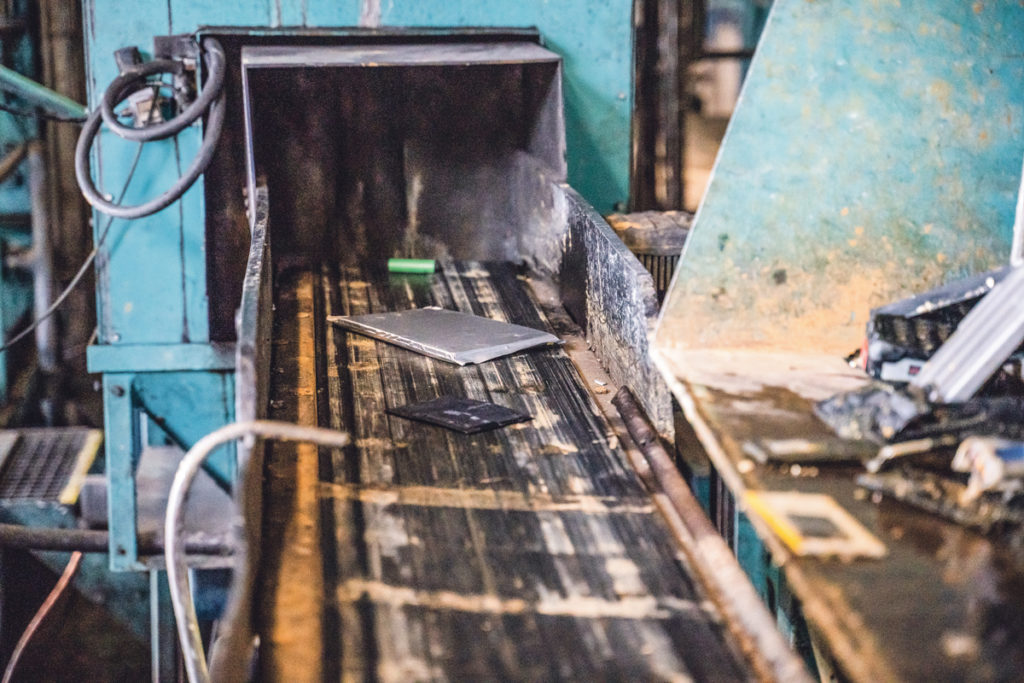
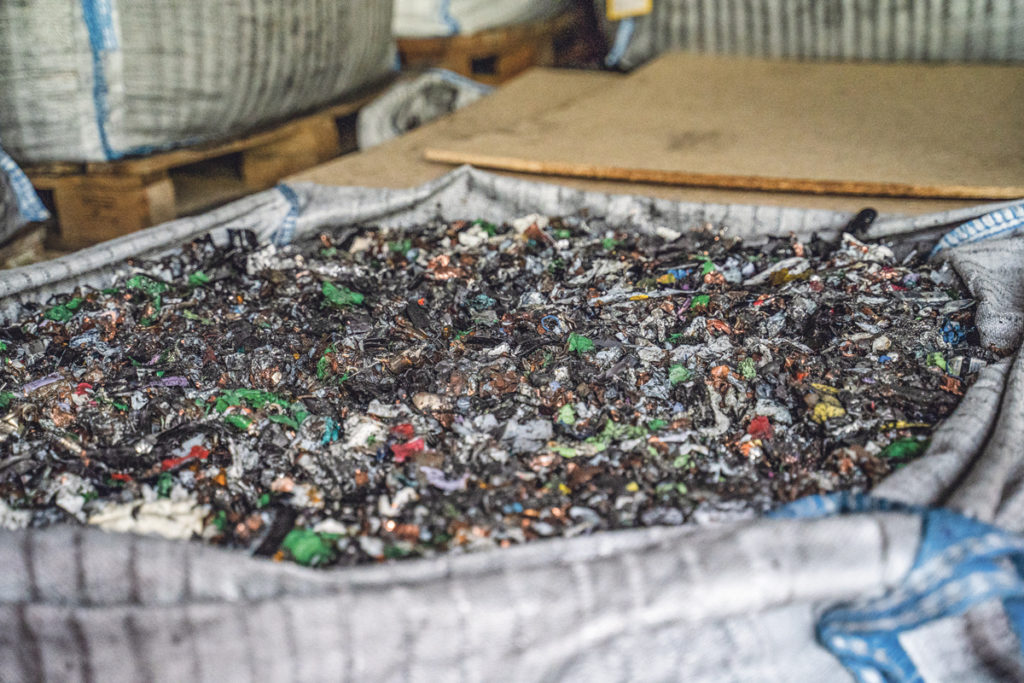
De l’avis de ce pro du recyclage, un système uniformisé serait des plus souhaitables. Mais le patron de Batrec se montre compréhensif: «Les batteries que nous récupérons aujourd’hui ne sont pas conçues pour être recyclées de manière aussi efficace que possible. Il faut dire qu’autrefois, les fabricants avaient bien d’autres soucis.»
Seconde vie
Chez Batrec, après le démantèlement, des représentants de chez Libattion, une autre entreprise situé à Glattbrugg et avec laquelle Batrec a mis sur pied une joint venture (lire en p. 16), vérifient quels modules peuvent encore servir. Et il y en a énormément! Pour les constructeurs automobiles, une batterie est en bout de vie lorsque sa capacité est de 80%. Bien entendu, ces batteries peuvent encore servir, sous le capot d’un chariot élévateur, d’une voiture de golf ou encore comme une simple batterie murale. Dans le cas contraire, on la décharge de façon contrôlée par court-circuit ou complètement en la plongeant dans un bain d’eau pendant plusieurs semaines avant de la préparer pour le broyage. A ce propos, l’électrolyte, le composant inflammable de toute batterie lithium-ions, requiert une attention particulière lors du recyclage. Effectivement, la moindre tension électrique, la moindre étincelle et tout s’enflamme. Duesenfeld noie donc la broyeuse étanche à l’air dans une atmosphère d’azote. Chez Batrec, on a opté pour un milieu liquide.
Générateur de matières premières, tout ce processus permet, bien entendu, de réduire énormément l’empreinte carbone lors de la fabrication de nouvelles batteries, jusqu’à concurrence de 40%, selon certains experts.
Une autre vie après la voiture
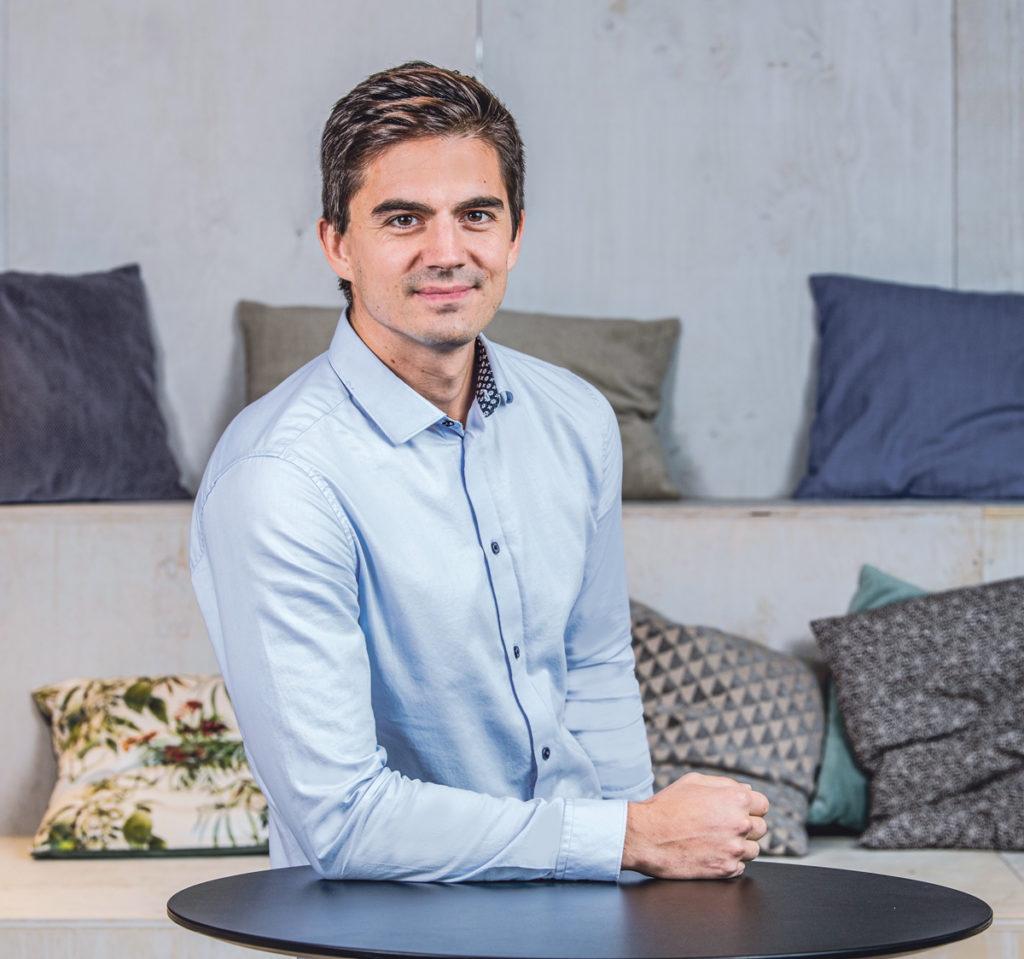
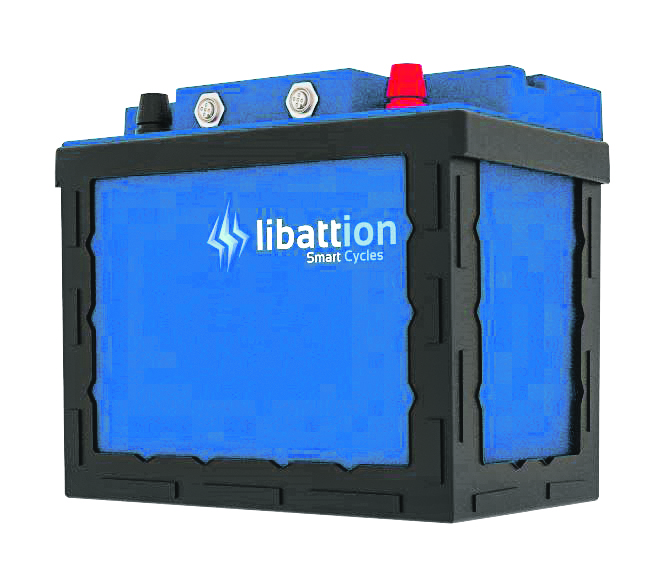
CIRCUIT FERMÉ Les batteries au lithium-ion des véhicules électriques sont loin d’être usagées après leur première utilisation. La start-up zurichoise Libattion leur offre une seconde vie.
Les batteries au lithium-ion constituent actuellement la solution la plus écologique et la plus performante pour les applications mobiles. C’est Rolf Widmer, de l’Empa, qui l’affirme. Elles sont peu encombrantes et ont une longue espérance de vie. A une autre échelle, cette technologie s’impose depuis des années dans les smartphones. Mais, avec le boom des voitures électriques, la production de ces batteries devient de plus en plus gourmande en ressources et en énergie.
En partant du principe que l’espérance de vie primaire d’une batterie est de l’ordre de 10 ans lorsqu’elle est utilisée pour animer un véhicule électrique, et sachant que l’électromobilité s’imposera réellement dans une décennie au plus tôt, la première vague de batteries usagées nous inondera probablement dans 20 ans. «Nous devons nous y préparer», en conclut Stefan Bahamonde, le patron de Libattion.
La start-up zurichoise coopère avec l’entreprise de recyclage Batrec (voir page 14) pour redonner vie aux batteries usagées. Contrairement à ce qui se fait lors d’un recyclage, ces dernières sont testées et les cellules encore fonctionnelles sont transplantées dans un nouveau système. Chez Libattion, ce sont les «e-bricks» standardisées, que l’on trouve déjà sur le marché. Les e-bricks peuvent déjà être louées sur la base d’un modèle d’abonnement. «En offrant une possibilité d’échange, nous garantissons l’efficacité constante du système», explique le patron de la start-up. «Par principe, nous ne récupérons que les vieilles batteries ayant conservé au moins 80% de leur capacité d’origine.» Selon le domaine d’application, qui va des chariots élévateurs et machines de nettoyage aux applications stationnaires comme les batteries de stockage d’énergie solaire, les exigences peuvent être encore plus hautes.
Grâce à une gestion élaborée, le nombre de cycles de recharge des e-bricks serait identique à celui des batteries au cours de leur durée de vie primaire, pour un poids supérieur d’environ un quart. Car, dans le cas des vélos électriques, notamment, il est fréquent que seul le système de gestion de la batterie présente une défaillance, les autres éléments étant le plus souvent encore opérationnels.
Premières expériences
En Suisse, Libattion est actuellement le seul fournisseur de telles solutions. Les e-bricks de la start-up zurichoise proviennent encore principalement de batteries de vélos électriques usagées, achetées directement à Batrec. Mais des pourparlers avec un constructeur automobile sont en cours.
On admet généralement qu’une batterie de voiture électrique est usagée quand elle tombe en dessous de 80% de sa capacité initiale. Cela signifie par exemple que l’énorme batterie d’une Tesla (100 kW), une fois recyclée, aura 80 kWh à disposition, ce qui correspond à plus de deux batteries de VW e-Golf neuves. Comme les constructeurs sont légalement tenus de reprendre les batteries usagées, nombre d’entre eux ont déjà mis en œuvre leur propre programme de seconde vie. Audi fait ses premières expériences avec des chariots de manutention alimentés par des batteries d’e-tron usagées. Chacun des 36 modules est testé pour déterminer s’il est encore utilisable et 24 d’entre eux sont intégrés dans un nouveau pack.
Chez Daimler, les batteries usagées doivent être réutilisées pendant 10 ans, en tant que tampons dans les réseaux électriques. En coopération avec le géant du recyclage Remondis, les batteries de Smart EQ stockent donc l’énergie excédentaire du réseau électrique et la restituent en cas de besoin. Chez BMW, on recherche une solution similaire en stockant de l’énergie éolienne et solaire dans 700 batteries d’i3 usagées et neuves. VW, qui a lancé récemment la première «power bank» destinée aux voitures électriques, mise sur une solution mobile permettant la mise en place rapide et flexible d’une infrastructure de recharge dans des endroits isolés.
Grande diversité
La situation des batteries de voitures électriques – contrairement à celle des vélos où le même type de cellule est utilisé partout – est d’autant plus complexe qu’il existe une grande diversité en matière d’architecture et de chimie des cellules. De ce fait, Libattion n’est actuellement pas en mesure d’incorporer les divers types de cellules dans la forme standardisée de l’e-brick. «Notre objectif est d’obtenir un même type de batterie auprès du plus grand nombre de constructeurs possible, que nous pourrons ensuite standardiser», explique Stefan Bahamonde. «Pour l’instant, nous travaillons encore sur la base de projets. Si une batterie de 10 kWh est nécessaire pour stocker de l’énergie solaire, l’e-brick sera élaborée spécialement à cet effet.»
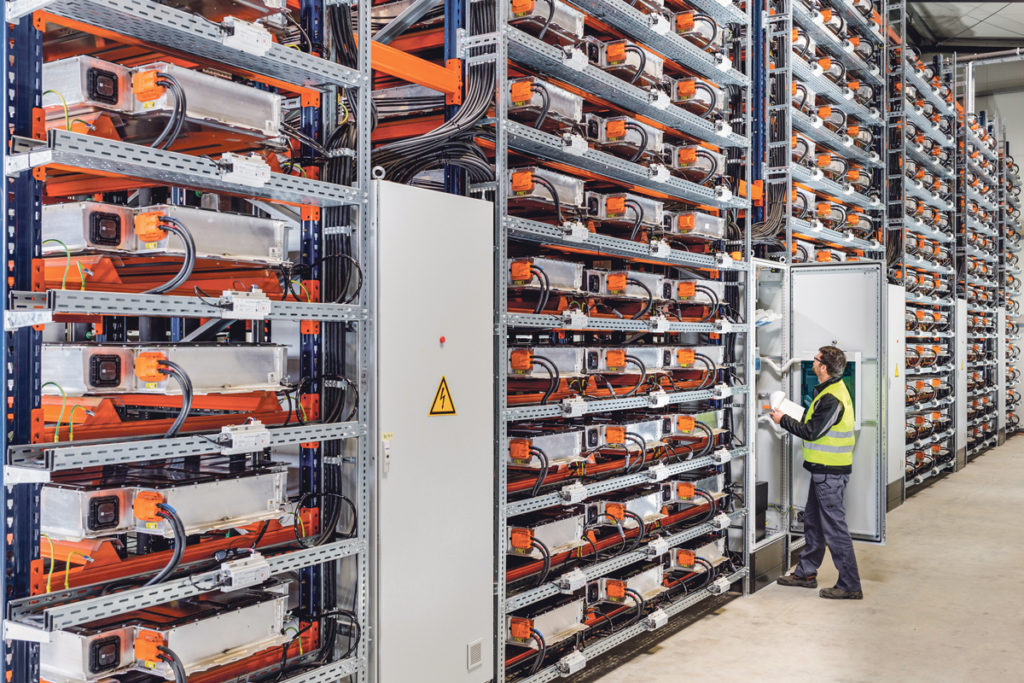
Recyclage incontournable
Sous réserve d’un vieillissement normal, la capacité des dispositifs de stockage d’énergie diminue au fur et à mesure des cycles de recharge. Un processus comparable à celui qui se produit avec les smartphones, dont la batterie s’épuise littéralement après quelques années d’utilisation. L’accumulateur peut toujours être rechargé, mais sa capacité est réduite à un point tel que l’appareil n’a plus qu’une autonomie très limitée. «Il y a inévitablement un point de rupture, mais cela dépend beaucoup de la chimie des cellules. On évalue ce chiffre entre 30 et 50% de la capacité initiale de la batterie», explique Stefan Bahamonde. «Une batterie au lithium-ion doit ensuite être recyclée, la boucle est ainsi bouclée.»λ