Les procédés de fabrication additive – également connus sous le nom de construction en couches ou production de formes libres – font partie intégrante de la réorientation globale de l’ingénierie automobile. Ils aident, en effet, les constructeurs automobiles à rester compétitifs, puisqu’il permettent de sortir des composants à moindres coûts. Le terme d’impression 3D se réfère à un ensemble de procédés du domaine de la fabrication additive. Contrairement aux méthodes de fabrication soustractive, l’approche additive se réfère à la production d’objets par accumulation de matière, généralement couche par couche. Dans les procédés soustractifs, une part de la matière première est enlevée par fraisage, tournage ou perçage afin de créer la forme souhaitée.
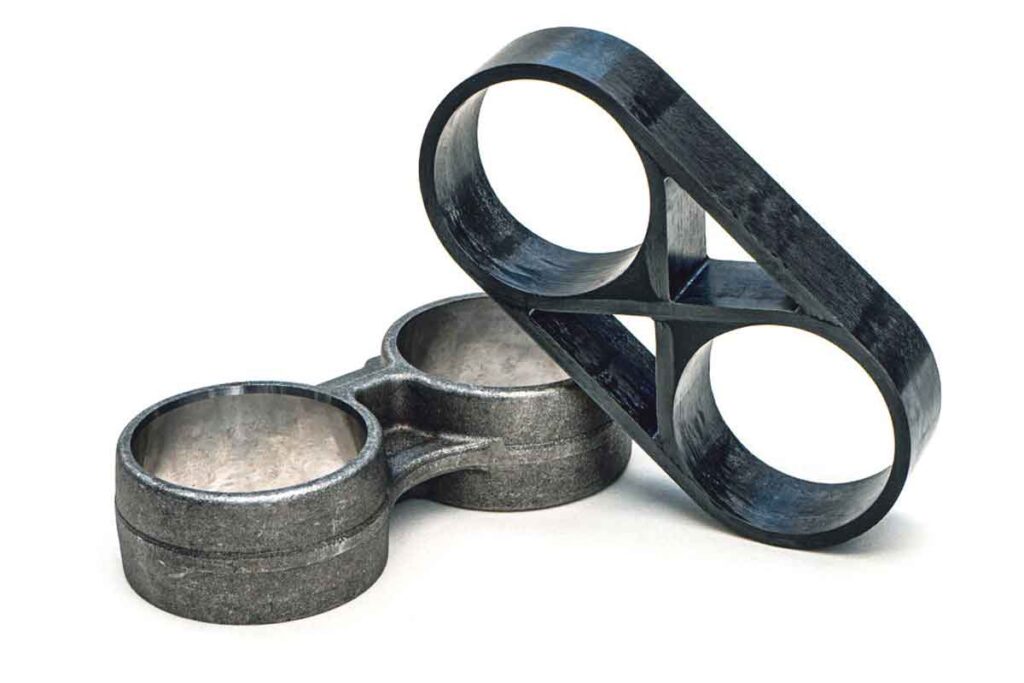
«Rapid manufacturing»
Alors que la modélisation traditionnelle faisait appel à des ébauches en argile, en bois ou en mousse, les prototypes soutiennent désormais directement la production. Suite à un brevet déposé en 1980, le premier procédé additif, la stéréolithographie, a été développé en 1984 puis commercialisé peu après. Sa rapidité de réalisation permet la fabrication de prototypes à faibles coûts pour le développement de produits. Certains procédés sont même appliqués pour la fabrication de pièces définitives, sous le vocable «rapid manufacturing». Globalement, les différents procédés de fabrication additive ont tous connu un véritable boom ces dernières années. La raison? L’expiration du brevet sur le procédé d’impression FDM (Fused Deposition Modeling) et l’émergence des imprimantes 3D «open source». L’idée de pouvoir fabriquer de nouveaux produits à domicile, en peu de temps, présente forcément beaucoup d’attrait, raison pour laquelle elle s’est aujourd’hui imposée dans
de nombreuses industries grâce à ses possibilités presque illimitées. De nouveaux matériaux sont constamment développés, de sorte que l’éventail des applications ne cesse de s’élargir.
Après la recherche scientifique, la médecine, l’aérospatiale ou encore le secteur du bâtiment, la fabrication additive a trouvé un nouveau débouché dans l’industrie automobile, où les constructeurs l’utilisent notamment pour le prototypage rapide de moteurs et d’autres composants mécaniques tels que les carters. Le processus d’optimisation conceptuelle devient à la fois plus facile et plus rapide, puisqu’un nouveau prototype peut être imprimé directement à partir d’un fichier informatique. De plus, une imprimante 3D est capable de créer des éléments à la géométrie très complexes, ce qui exigeait auparavant des ressources incomparablement plus élevées.
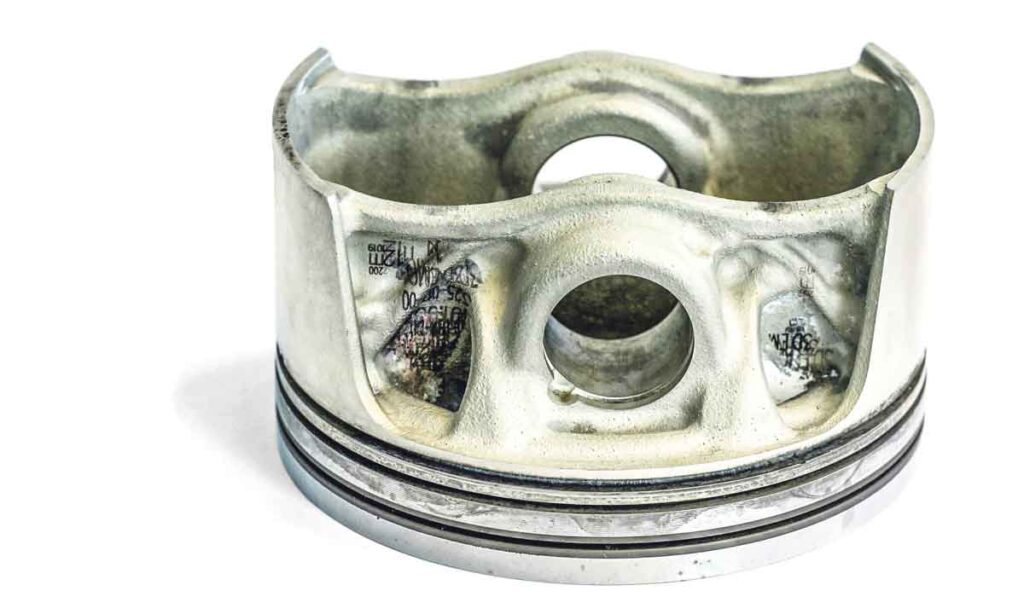
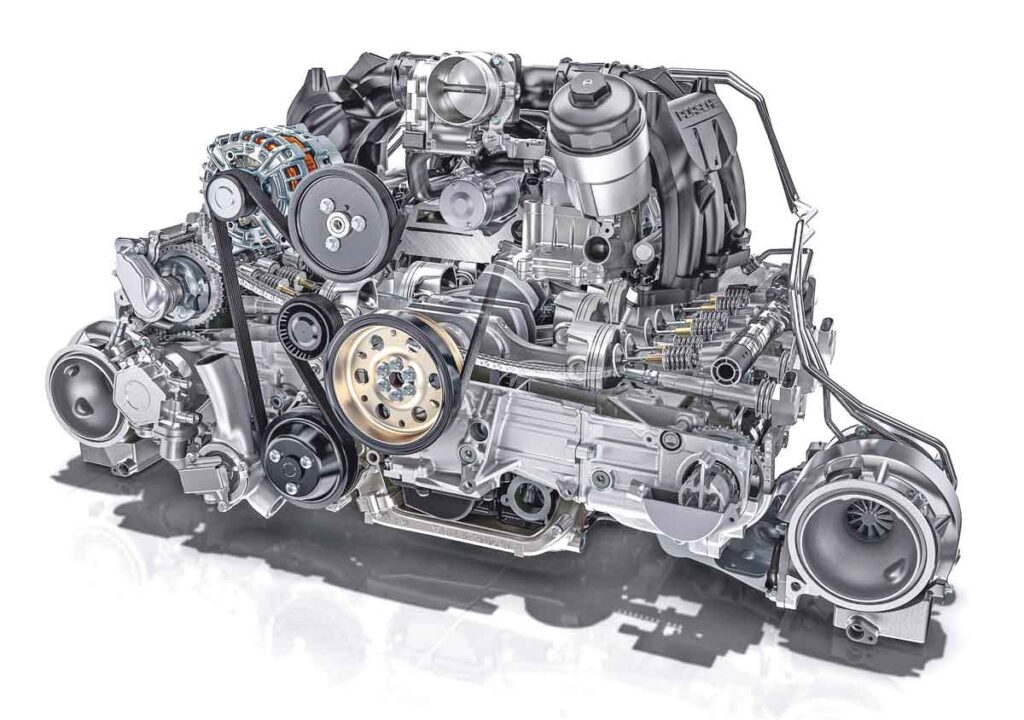
Métaux et plastiques
La fusion sélective au laser SLM (Selective Laser Melting) est un procédé de fabrication additive pour des composants métalliques, qui ne nécessite ni moules ni outils. La pièce est réalisée couche par couche à partir de poudre métallique solidifiée par microsoudure laser. La structure en couches est très bien adaptée aux géométries complexes, dont l’usinage coûterait bien plus cher. Il est même possible de combiner des ensembles complexes d’un seul tenant. En principe, le processus SLM peut traiter tout alliage métallique pouvant être soudé. Cependant, différentes technologies de traitement s’imposent en fonction du matériau. Outre des temps de développement plus courts, la SLM permet généralement d’obtenir des avantages en matière de poids et de coût. Toutefois, le processus ne convient pas à toutes les applications, ni à toutes les formes de composants. Ainsi, pour des éléments plus simples, les techniques de fabrication conventionnelles restent souvent plus rentables. Dans ce cas, l’impression 3D n’est utilisée que si elle peut apporter une valeur ajoutée fonctionnelle. La qualité de la poudre métallique est déterminante pour la fiabilité du processus SLM. Entrent ici en jeu la composition chimique, mais aussi la forme des particules et leur taille, plus ou moins homogène. Ces facteurs influencent la masse volumique apparente, la fluidité du matériau et, par conséquent, sa structure.
Les procédés d’amoncellement de matière concernent aussi le façonnage d’éléments en plastique. En plus de la stéréolithographie, les méthodes possibles sont le jet de liant et le frittage sélectif au laser. Le plastique étant le plus souvent utilisé pour la conception d’ébauches, la résistance de l’objet n’est pas un facteur prioritaire. Quant aux règles de fabrication, elle diffèrent bien évidemment de celles de l’impression 3D en métal.
L’intérêt croissant des constructeurs automobiles
Il y a quelques semaines, BMW a officiellement ouvert l’Additive Manufacturing Campus, dédié à la production de prototypes et de composants de série. Ce laboratoire développe aussi de nouvelles technologies d’impression 3D et forme des spécialistes dans le domaine. BMW n’a toutefois pas attendu l’inauguration du site pour démarrer la production, puisque l’an dernier, pas moins de 300 000 pièces sont déjà sorties des ateliers de fabrication additive. Les Bavarois tablent sur un potentiel de réduction des coûts pouvant atteindre 50% pour la production en série.
Au sein du groupe Volkswagen, l’impression 3D est à l’origine des sorties d’échappement en titane de la Bugatti Chiron Pur Sport, qui se distinguent par leur paroi très fine et leur résistance aux températures élevées. Effectivement, la fabrication additive a permis d’alléger autant que faire se peut les lignes d’échappement, situées en retrait de l’essieu arrière, et ce afin de permettre au bolide d’afficher une répartition quasi parfaite des masses suspendues. De son côté, Mercedes a tout spécialement recours à la fabrication additive dans le domaine des voitures classiques. La division Mercedes-Benz Classic réalise en impression 3D des pièces détachées en métal, en plastique ou en caoutchouc, comme par exemple la base du rétroviseur intérieur en aluminium de la 300 SL, ou le porte-bougie en polyamide 12. Il est à noter que les patins de toit ouvrant de plusieurs séries de modèles sont également fabriqués par cette technique d’amas de matière. A Zuffenhausen (Porsche) aussi, les imprimantes 3D interviennent dans la fabrication de prototypes et la production de pièces détachées pour des sportives classiques. Avec ses partenaires Mahle et Trumpf, Porsche a même développé de nouveaux pistons pour le moteur hautes performances de la 911 GT2 RS (modèle 991), c’est-à-dire des composants étant intensivement sollicités.
Les éléments fabriqués par addition de matière pèsent 10% de moins que les pistons forgés d’origine. En outre, ils disposent d’un canal de refroidissement intégré dans la couronne du piston qui est tout simplement impossible à réaliser par usinage conventionnel. L’imprimante 3D est également utilisée dans le process de fabrication d’éléments des sièges baquets des 911 et autres 718, ainsi qu’à la reproduction d’une vingtaine de pièces pour les Porsche classiques. Sans compter diverses pièces de petite série destinées à la compétition.
«Les limites du laboratoire d’impression 3D sont celles de l’imagination», peut-on entendre chez Seat. Outre les nombreuses possibilités de conception, l’atout majeur de l’impression 3D réside dans la rapidité d’exécution des pièces. Chez Seat, 80% des objets imprimés sont des prototypes pour le développement de véhicules, mais la fabrication additive sert aussi à produire des outils et des éléments pour la chaîne de montage ainsi que des logos pour les voitures d’exposition et de démonstration. Comme chez les autres constructeurs, la marque espagnole exploitera la fabrication additive de manière toujours plus intensive.
Les différents procédés d’impression
En matière de fabrication additive, il existe plusieurs types de procédés spéciaux qui dépendent du matériau à traiter ou de l’application visée. Les plus importants sont les suivants.
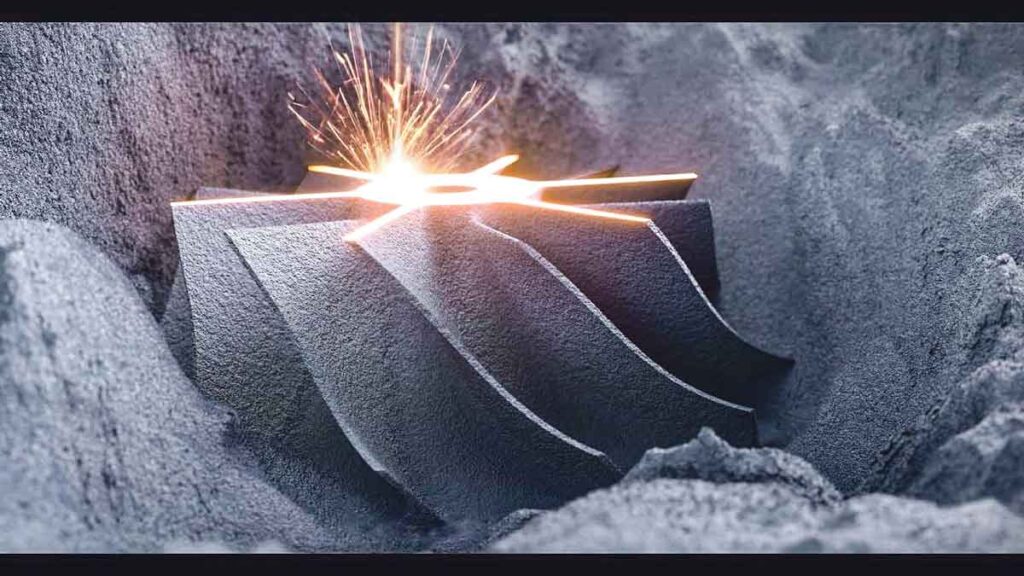
«Selective Laser-Melting»: La fusion sélective au laser SLM (Selective Laser Melting) est un procédé d’impression 3D dans lequel une poudre de métal est fondue, couche par couche, par un laser. Les composants sont reliés à un support qui maintient solidement l’ensemble et permet de dissiper efficacement la chaleur pendant la production. Le laser fait fondre la poudre de métal à des températures pouvant atteindre 1250 °C.

«Multijet-Modeling»: La modélisation «polyjet» ou «multijet» s’apparente quelque peu au jet d’encre: une tête d’impression se déplace au-dessus de la plateforme de construction et pulvérise de fines gouttelettes de plastique liquide. Le matériau est aussitôt irradié par la lumière UV et durcit presque simultanément.
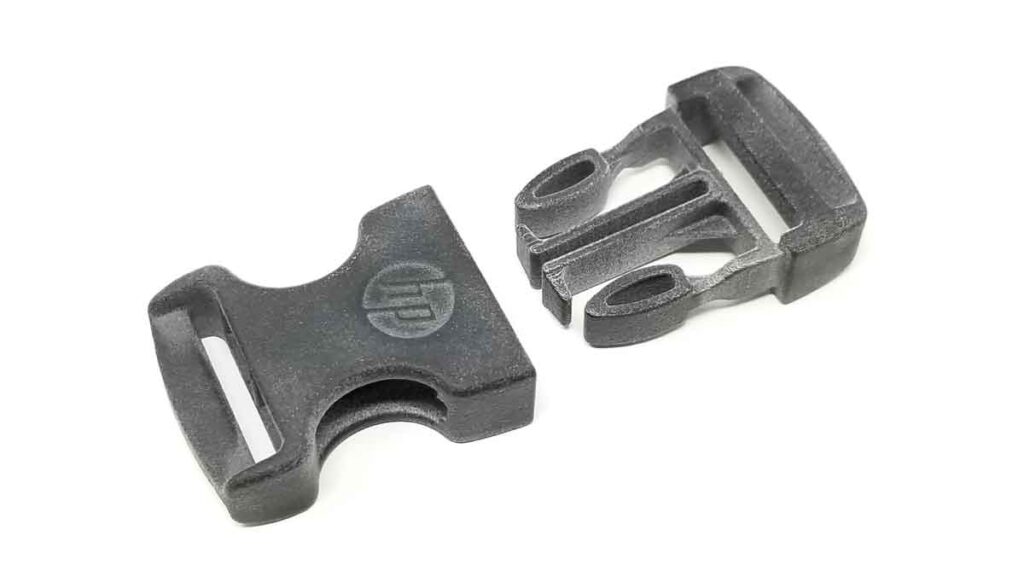
«Multijet Fusion»: La fusion multi-jet est un procédé d’impression 3D relativement nouveau dans lequel du plastique en poudre est incorporé à très grande vitesse à des objets 3D. Contrairement à la fusion sélective et au frittage laser, les différentes couches ne sont pas fusionnées grâce à un rayon; la poudre est imbibée par deux liquides liants et fusionnée par l’énergie thermique des lampes infrarouges. Il en résulte un objet 3D à la surface lisse et régulière.
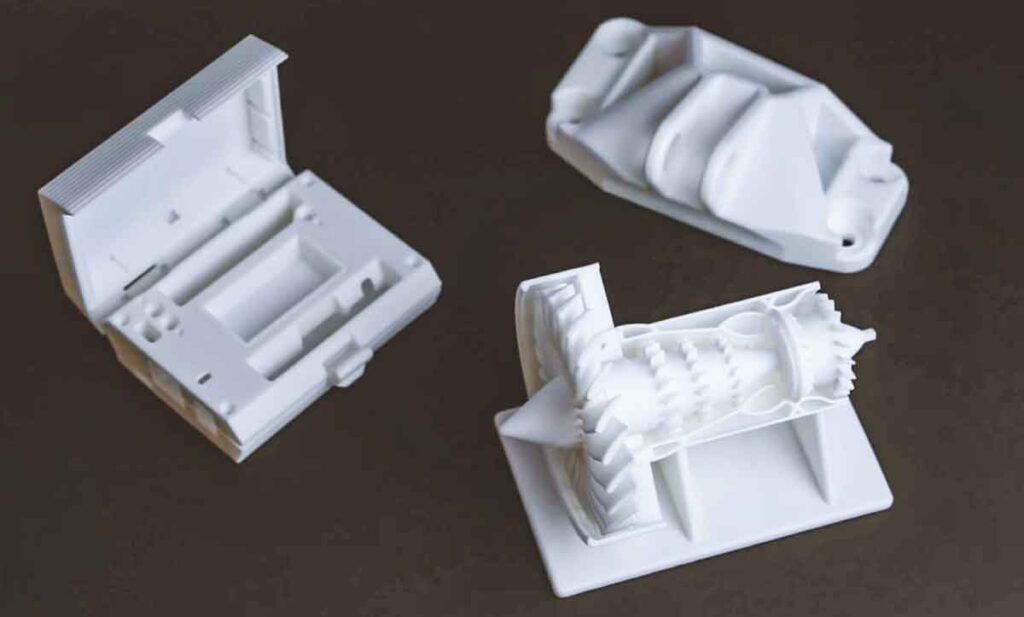
Frittage laser sélectif: Le frittage laser sélectif est un principe de fabrication dans lequel un plastique en poudre est fusionné et intégré à une structure en trois dimensions. Une très fine couche de poudre thermoplastique est chauffée au moyen d’un laser infrarouge, jusqu’à la limite du point de fusion. Elle est ensuite fondue. Par la suite, la plateforme de construction est abaissée d’une épaisseur de couche et le processus de fabrication peut recommencer.
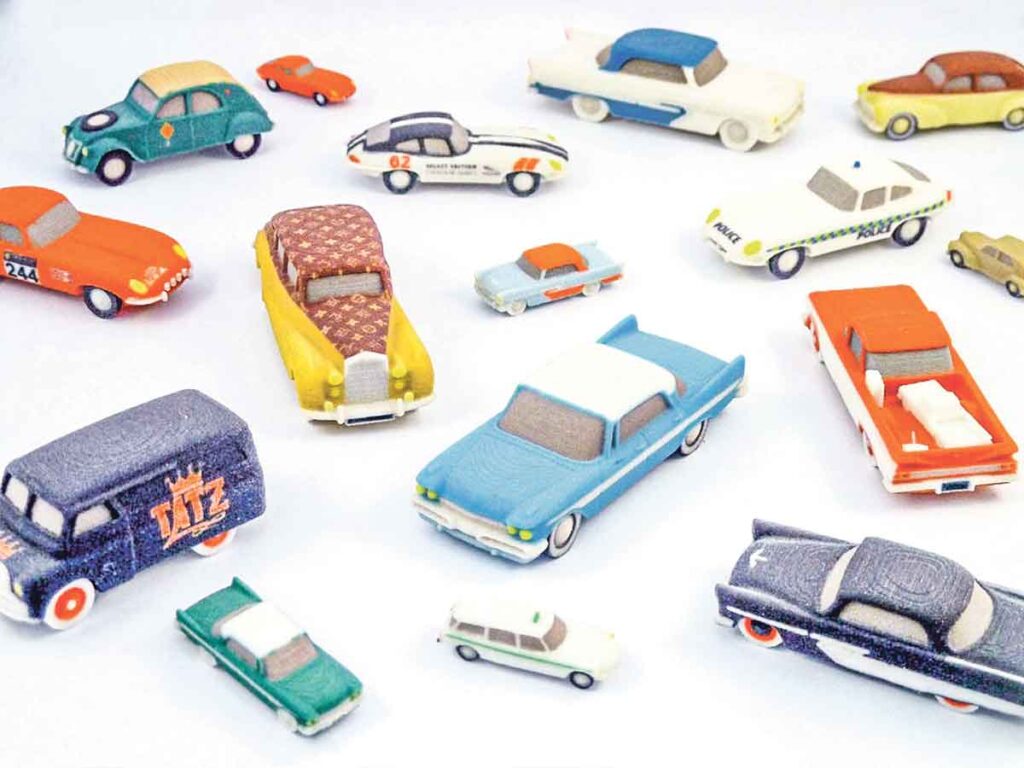
«Binder-Jetting»: Dans le procédé du jet de liant, la poudre plastique est appliquée en couches et liée par un liquide. Ce procédé permet la création d’objets tridimensionnels de formes extrêmement diverses, tout en s’affranchissant des structures de support. Contrairement aux procédés thermiques tels que le frittage sélectif au laser, le matériau est traité par une chimie à froid. Ensuite, l’ensemble de l’assemblage durcit dans une chambre thermique puis l’objet est finalement bombardé de billes de verre qui lui confèrent une surface compacte.

Stéréolithographie: Développée dans les années 1980, la stéréolithographie est un processus additif dans lequel un plastique liquide, appliqué en couches de 0,025 mm à 0,250 mm d’épaisseur, est durci localement par la lumière UV. A chaque cycle, la machine abaisse la plateforme de construction d’une épaisseur de couche. A noter que la surface est nappée de liquide, puis la phase de durcissement a lieu.